The cooling process in a nonwoven fabric production line is essential to set the structure and properties of the fabric after it has undergone heat-related processes. Cooling is typically employed after stages like melt spinning, thermal bonding, or other thermal treatments. The specific methods used for cooling in a nonwoven fabric line may vary depending on the production technology and the type of nonwoven fabric being manufactured.
Here are common ways in which the cooling of nonwoven fabric is handled:
- Air Cooling:
- One of the most common methods involves using ambient air for cooling. After the fabric undergoes a thermal process, it is exposed to controlled airflow to dissipate heat. This can be achieved through conveyors or open-air passages, allowing the fabric to cool gradually.
- Cooling Drums or Rollers:
- Some nonwoven fabric lines utilize cooling drums or rollers that come in direct contact with the fabric. These drums or rollers are often chilled, and as the fabric passes over them, heat is transferred to the cool surface, facilitating rapid cooling.
- Water Cooling:
- Water cooling systems can be employed, especially for fabrics produced through processes involving water, such as spunlaid or wet-laid methods. Water is used to cool and solidify the fabric, and excess water is then removed through squeezing or other means.
- Air-Cooled Conveyors:
- Conveyors designed with air-cooling systems can be used to carry the fabric through a cooling chamber. The conveyor system may incorporate fans or blowers that direct cool air onto the fabric, aiding in the cooling process.
- Cooling Chambers or Tunnels:
- Cooling chambers or tunnels with controlled temperature and airflow conditions may be integrated into the production line. Fabrics pass through these chambers, allowing for uniform and controlled cooling before moving to the next processing stage.
- Vacuum Cooling:
- In some cases, vacuum cooling may be employed. nonwoven fabric line This method involves creating a vacuum environment around the fabric, which promotes rapid cooling by reducing pressure and facilitating the removal of heat.
- Combination of Cooling Methods:
- Many nonwoven fabric lines use a combination of cooling methods to optimize the cooling process. For example, initial air cooling may be followed by contact with cooled rollers or drums for further temperature reduction.
- Cooling Fans or Blowers:
- Dedicated cooling fans or blowers may be strategically placed along the production line to provide localized cooling. These devices direct cool air onto specific sections of the fabric to ensure effective cooling.
- Controlled Ambient Conditions:
- The overall ambient conditions within the production facility, such as temperature and humidity, may be controlled to create an environment conducive to efficient fabric cooling.
- Length of Cooling Section:
- The length of the cooling section in the production line is carefully designed to allow sufficient time for the fabric to cool uniformly. The speed of conveyors or other transport systems is adjusted to ensure adequate cooling time.
Effective cooling is crucial to stabilize the structure and properties of the nonwoven fabric, preventing deformation or damage that could occur if the fabric is not adequately cooled. The choice of cooling method depends on the specific manufacturing process and the characteristics desired in the final nonwoven fabric product.
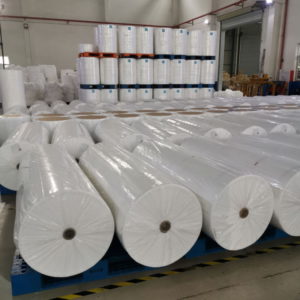